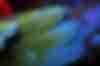
ISOPON PM is an auxiliary specifically engineered for equipment cleaning with effective dispersing and anti-oligomer action as well as reducing action: a multi-purpose product providing several advantages that make Isopon PM one of our best sellers appreciated all over the world.
1 ACKNOWLEDGING THE ISSUE
Dyeing equipment staining /dirtiness build-up after daily activity in a textile mill is a common problem. The dirtiness is mainly due to:
> Dyestuffs
> Insoluble fatty derivatives
> Inorganic substances
> Oligomers
> Sizing agent
Cleaning is an integral part of machinery maintenance, and neglecting it means shortening the life of the systems increasing the probability of breakdowns and machine downtime.
On the contrary, constant and regular cleaning management guarantees more efficient systems and, consequently, more productivity.
Clean and efficient machinery guarantees perfect, defect-free final products.
2 Beyond cleaning: optimizing the process
The cleaning process means a temporary stop in the production and may feel like a waste of time: we already stated the importance of this frequent a thorough process therefore, we developed a solution to optimize it with ISOPON PM.
ISOPON PM is a hydro-soluble combination of a biodegradable dispersing agent, a natural reducing structure, and surfactants that allow achieving outstanding equipment cleaning in a synergic way.
It’s a high foaming, pH-insensitive surfactant, suitable for cleaning jets and other equipment for the discontinuous process.
Isopon PM can solubilize the polyester oligomers in alkaline media, avoiding spots formation due to their redeposition on the goods and into the machinery.
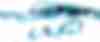
3 Isopon PM and sustainability
The most relevant certification bodies approve Isopon PM; it is solvents and APEO free.
It’s recognized worldwide as the multipurpose product to achieve relevant savings of:
ENERGY > More efficient heating device
TIME > reduced stop-time for cleaning
WATER > less water needed for cleaning
COSTS > The faulty goods are strongly reduced (less re-worked fabrics), and the equipment is better preserved
4 Some tests results
Bath Recipe:
- 0.2% C.I. Disperse Blue 183
- 0.3% C.I. Disperse Red 159
Filtering at 90°C
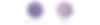
Solution containing oligomer.
- Bath heated to 130°C
- Held bath at temperature for 20 min.
- Bath cooled to 90°C.
- Bath filtered ON BLACK PAPER
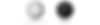
BEFORE TREATMENT
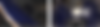
AFTER CLEANING PROCESS WITH ISOPON PM
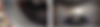
5 Appendix: the oligomers deposits.
During the polyester dyeing step, oligomers’ precipitation increases with heat-setting, high dyeing temperatures, long dyeing time, and short liquor ratio.
On the other hand, it decreases by using a suitable oligomer dispersing agent, with short dyeing time, high-temperature draining of the dyeing bath, and alkaline reduction clearing.
The problems caused by oligomer precipitation are many, mostly related to uneven dyed substrates, dusty deposits both on the fibre and on the machine, resulting in faulty goods and frequent stops for the cleaning process.
The oligomers formation can be reduced in a sustainable way with the combined use of Permulsin AO300 during the dyeing step and Isopon PM during the cleaning step.
Both the products are bluesign approved, ZDHC certified, Listed by Inditex, GOTS approved and GRS compliant.
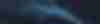
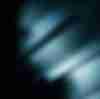